STAR Electro-Hydraulic Servo-Valves utilising our now famous sapphire technology and other modernised components to eliminate ball glitch and significantly reduce contamination failure; saving you downtime and money!
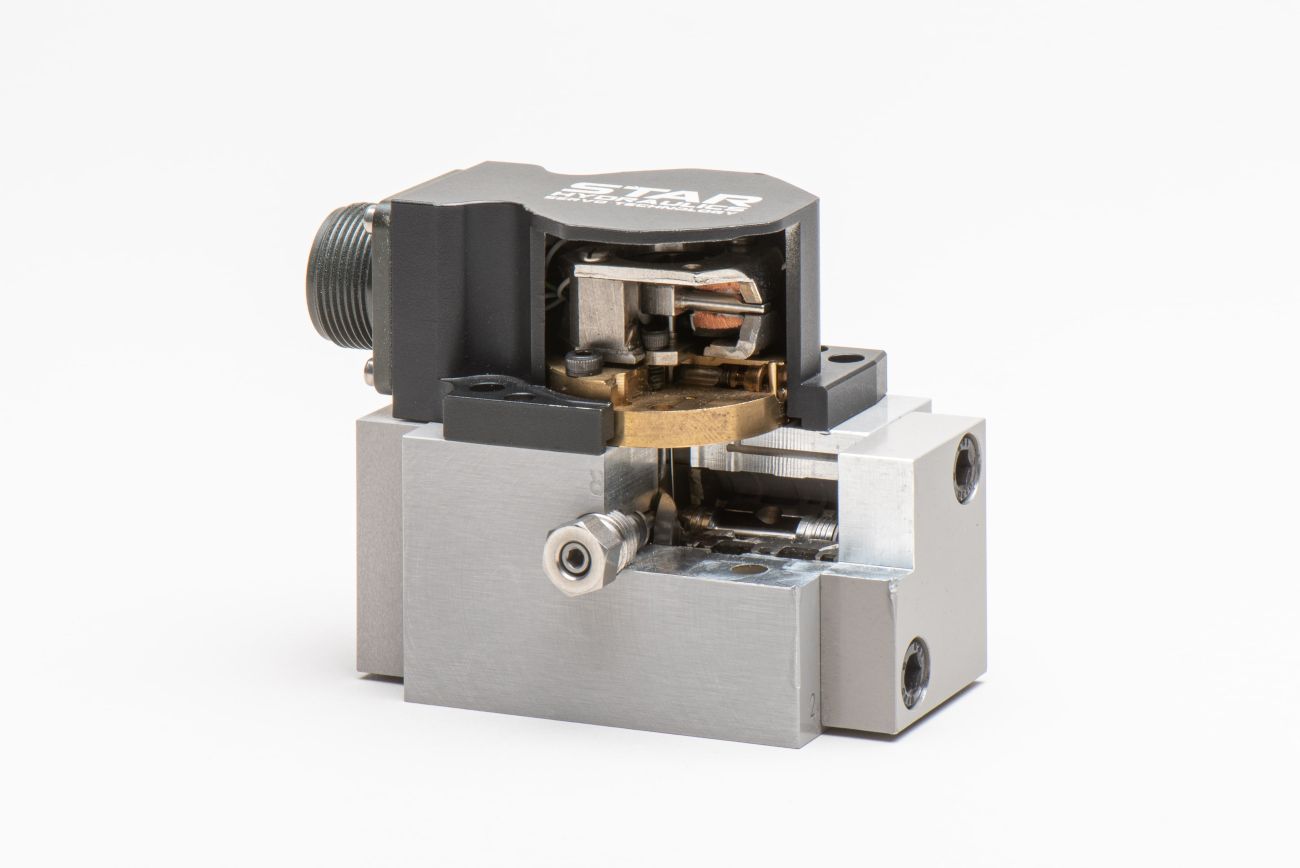
The key to our success
The key to our success is down to the many years of product development in both product design and materials selection, which enables our customers to improve operational life with consistently high performance. Cost of ownership is enhanced not only through lower initial costs, but also through minimal valve downtime.
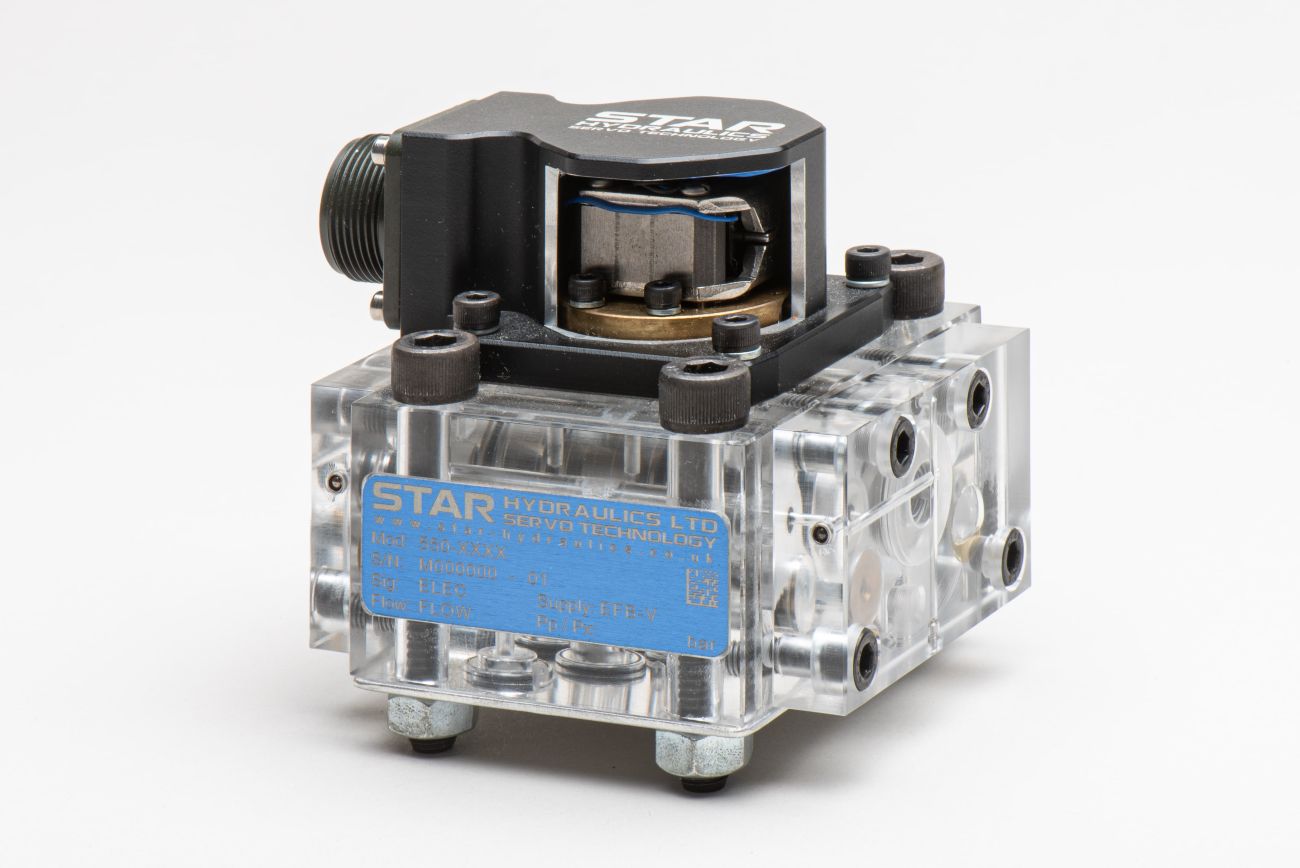
What we can offer
We pride ourselves on the support that we can offer, not only to the OEM but also to re-sellers and end-users in all market sectors around the world in conjunction with the "STAR International Distribution and Service Partner Network”.
Electro-hydraulic servo valves have been available for many decades but for many users early technology was associated with high running costs and down time due to weaknesses in valve design and/or poorly designed systems. Early industrial users were also lacking in knowledge and expertise relating to fluid monitoring and cleanliness.
This was the catalyst for the birth of STAR Hydraulics who started business by offering to service and repair servo valves at a time when many OEM’s saw little merit in extending the working life of broken servo valves. It became very clear at the out set that there was a pattern of common malfunctions of existing servo valve design such as 'Ball Glitch”, 'Inlet Orifice Erosion”, 'Inlet Orifice Release”and 'Flexure Sleeve Fatigue” which were all contributing to down time asperformance deteriorated. These were key factors in our re-engineering and re-manufacturing programme which has won us acclaim around the world on many prestigious applications where life extension and greater reliability has subsequently been achieved.
To those interested in the single issue of ball wear. This is not simply about just implementing hard exotic materials to make something last longer but also an appreciation of the way a servo valve performs and fails in the imperfect world of hydraulics.
The development programme for the sapphire feedback design originated in aerospace structural test systems with an aim to provide a servo valve that could last 5 years or more whilst operating continuously 24 hours a day, 7 days a week. Although the test engineers had striven to ensure the system components were manufactured, assembled and operated under strict cleanliness and temperature guidelines the mechanical wear within the servo valves that they used at the time would always surface within a short period of the total test window. Given that such testing programmes can consist of hundreds of servo channels, the test time lost and the high financial cost of stopping the test, to first evaluate the fault, fix it and then set the test up again, highlighted an expensive weak link associated with using high performance control valves… something needed to change.
There have been a number of iterations of our mechanical feedback design over the years owing to our understanding of the environmental conditions that exist in the real world. The current sapphire ball-in-slot arrangement has better operational qualities for a number of reasons: -
1) The ball-in-slot arrangement has no cavities in which fine particulates carried in the fluid are able to collect thus reducing the lapping effect between ball and slot that would normally accelerate mechanical wear.
2) The spool is not captive by the feedback mechanism avoiding the possibility of shear load on the wire created when flow forces apply torque to the spool.
3) Spool rotation actively reduces silting at the control ports and also increases the life of the metering edges when full annular ports are not utilised in the sleeve.
The above factors enable the feedback mechanism to remain in service longer in challenging environments, achieving billions of cycles.
Fluids are also a greater challenge nowadays as supply pressures are pushed ever higher and the necessity for non-mineral based fluids in many applications. Our sapphire feedback mechanisms are built to with stand Skydrol, water glycol and phosphate ester as well as extreme temperatures ranging from -45 °C to well above +145 °C, often seen during environmental testing of aircraft systems and components.
We are one of the few manufacturers to offer a repair service for other brands of electro-hydraulic servo valves and as a result have benefited from observations of valve failure due a wide variety of reasons. By improving component design and details such as our sapphire technology and using our experience with hydraulic systems and filtration we have enabled our clients to dramatically reduce the maintenance costs normally associated with such high end systems. End-users and OEM’s worldwide specify Star for some of the most demanding industrial applications.
Advantages of our STAR valves and service capabilities
* High quality sapphire ball in rotating spool eliminates ball glitch
* Star Torque Motor is multi-component which is economical to repair
* Flexibility to meet specific customer requirements
* Undertakes repair of competitors valves at very reasonable rates
* Short delivery standard lead times and priority service when required
* Consistent world-wide pricing structure
* Quality; our warranty rate currently stands at 0.03%
Benefits and Features
'Sapphire Technology” ball in slot design
Incorporated into Star designs since 1988
Many billions of cycles per service life
Increased spool life due to spool rotation
Ultra low coefficient of friction sapphire to steel
Feedback mechanism unhindered by spool rotation
Extended warranties available
Sapphire flow~
Ensuring first stage stability
Precisely matched flow properties
Long life in extreme environments
Custom spool lap & bushing
port geometries
Zero overlap
Overlap (closed center)
Underlap (open center)
Dual gain
Asymmetric gain
Special connectors
MIL-C-5015
MIL-DTL-38999
Conduit style male/female
Hermetic
Safety
Intrinsic safety
Class, Div & Zone coverage
Mechanical failsafe
Double & triple coil redundancy
Sealing materials
Nitrile
Fluorocarbon (Viton)
Ethylene-Propylene
Fluorosilicone
Facilities
Valve Assembly
This is a key function where very experienced staff assemble both new and repair valves in a clean environment.
Valve Testing Centre
Dedicated Test Room with Performance Qualification Test Rigs. Fluid cleanliness is better than ISO4406 Code 12/10/8 - NAS1638 Class 2
Total Manufacturing Facility
Precision Grinding
Charmilles Technologies Roboform EDM
Sunnen Honing and Lapping
Nikon Profile Projector
4 Axis Bridgeport CNC Machining Centre
4 Axis Doosan CNC Lathe
With 'State of the Art' Machining Facility Star Hydraulics are pleased to offer close tolerance machining services.
Why choose us?
- Over 40 years’ experience in research and development of electro-hydraulic servo valves
- British product manufactured entirely in the UK, British quality at its best
- A company run by engineers for engineers
- Committed to providing excellent customer service
- Technical support on hand and always ready to help you
- The customer is at the core of every business decision
- Worldwide delivery available
- Short delivery lead times
- Next day delivery on all ex-stock items
- Flexibility to meet specific customer requirements